A Beginner’s Guide to Welding
October 4, 2021
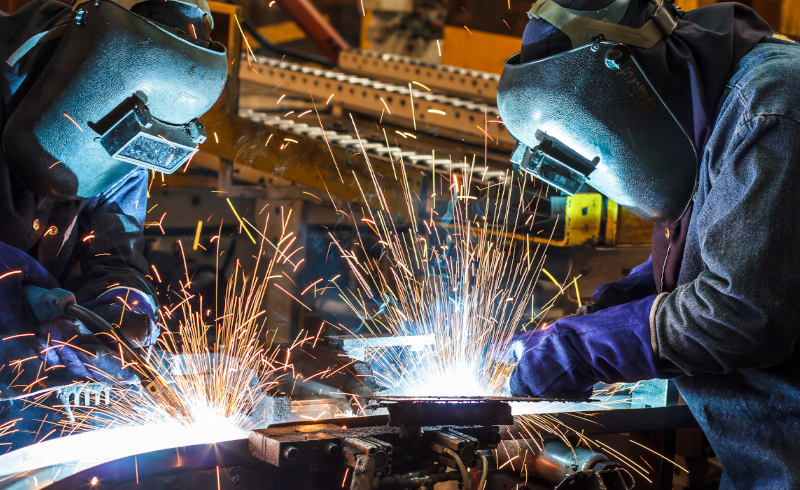
Welding forms a permanent bond between two pieces of metal. You can learn this skill with lots of practice and patience, so long as you take safety measures seriously.
Step 1: Choose Your Method
There are many welding methods, but if you’re just starting out, we recommend metal inert gas welding (MIG). MIG is a type of electric arc welding that melts a welding wire, or electrode, to partially melt the base metal. The parts then fuse together after the molten metals cool. MIG uses a weld gun that will feed wire from a spool while you pull a trigger. As the wire unspools, the welding gun will simultaneously supply a shielding gas to protect the metal from impurities in the air.
Step 2: Get Your Materials
Once you know what welding method you’ll use for a project, it’s time to collect all of your materials. Use the following checklist to make sure you have the right equipment:
- Welder: Investing in a good welder will make your projects easier to complete and your learning process more enjoyable. A wire-feed welder will use ordinary household current to produce a hot, high-energy electric arc. We’re talking thousands of degrees Fahrenheit! At Zaskoda Repair, we can help you find the right new or refurbished welder.
- Welding Wire: Welders take at least two different sizes of welding wire. You’ll want to use a thin welding wire at first, then increase the diameter of the welding wire as the material’s thickness increases.
- Shielding Gas: The correct shielding gas depends on your project, how deep you want your welds, and the type of torch you’re using. Check your welder’s owner’s manual for specific instructions on the type of gas your machine takes.
- Welding Cart: The welding machine is heavy! So, consider a welding cart to make your machine portable.
- Awl or Carbide Scribe: This is used to make cut lines.
- Right-Angle Grinder: A tool for grinding, beveling, or flattening welds, as well as preparing the surface.
- Miter Clamp or Magnet Square: A tool used to secure joints.
- Chipping Hammer and Wire Brush: This is used to clean up slag and spatter.
- Welding Pliers: This is necessary to trim welding wire and remove spatter from the welding gun nozzle.
- Auto-Darkening Helmet: Without a helmet, the brightness emitted from the arc-welding process will burn your eyes. Traditional welding helmets had a darkened viewing shade that meant you had to flip your mask up whenever you weren’t welding. Today, you can purchase a helmet with a clear lens that will automatically darken when it’s time to begin welding.
Step 3: Prepare Your Weld
After all of your materials have come in, it’s time to start welding! But think of the process as a game of monopoly: you can’t start collecting money from your hotels without building one house first.
- Get Your Metals Ready: Before you start melting metals, use your wire brush and acetone to remove dirt and oils from your welding materials. If you need to cut the metal, mark a line with your awl or carbide scribe, then use a metal-cutting chop saw, hacksaw, or grinder to cut along the marked line.
- Grind the Edges: Use a right-angle grinder to grind the edges of the metals you plan to join. This is known as chamfering. A chamfer is usually a 45-degree bevel between the adjoining edges of two materials. It creates a space for the filler and provides structural integrity for your weld.
- Position the Metals: Using a miter clamp or magnet square, secure the joints before you begin welding.
- Safety First: Do not start welding until you put on a welding jacket or apron, leather gloves, and a helmet. If you don’t have a jacket or apron, at least wear a long-sleeve cotton work shirt. Always wear work boots and remove jewelry from your wrists and neck. Wear safety glasses and a full-face shield even when you are grinding metals. And it’s a good idea to keep a fire extinguisher nearby.
Step 4: Layer Your Weld
- Keep Steady: A steady hand is the key to a clean weld. When possible, hold the welding gun with two hands or use the wrist of your “off” hand to guide the hand holding the welder. Before turning on the welder, practice your weld, creating a fluid, easily repeatable motion.
- Make Tack Welds: Make sure the wire electrode is sticking out between ¼ and ⅜ an inch. If the nozzle is clean, make a few tack welds along the joint to connect the base metals. Once the metals are tacked together, you can lay down your final weld beads.
- Lay the Final Beads: Move from left to right, keeping the weld gun at a 75-degree angle to the base. Spend one to two seconds laying down each bead and maintain a constant arc length. Look past the bright arc and concentrate on the edge of the weld puddle. At the end of the weld, pull the electrode back and allow the metals to cool.
If you’re just practicing on scrap metal, or if the weld is not visible on the finished project, then you’ve completed your weld!
Step 5: Grind Your Weld
If your weld is along an edge, or the weld is visible at the end of the project, you’ll want to grind the weld to create a smooth finish.
- Use a 36-grit grinding wheel attached to your right-angle grinder to grind along the weld path. If you don’t want to start over, look for orange sparks. Blue sparks indicate you’re pushing too hard and risk grinding through your weld.
- After grinding, you can use a zirconia flap disc for precise shaping and finishing.
Congratulations! You’ve completed your weld! Keep practicing to become familiar with the techniques. Over time, you’ll be more efficient and ready to tackle more challenging projects and types of welding. If you have questions about which welding machines are right for your specific projects and skill set, contact Zaskoda Repair today.